In the world of robotics, the demand for flexibility and adaptability has led to the exploration of soft materials. Inspired by nature, such as jellyfish, earthworms, fish, and the human body, researchers are now focusing on the development of “soft robots.” These robots, unlike their rigid counterparts, are designed to perform fine motor activities and interact with people in fields like nursing and medicine. A research team at the Department of Materials Science at Kiel University (CAU) showcases a hydrogel-based material that mimics the functionality of muscles, offering exciting new possibilities for soft robotics.
Responsive Hydrogel Material
Hydrogels, akin to those found in contact lenses, possess exceptional elasticity and are primarily composed of water, closely resembling human body tissue. The hydrogels in question here are termed “thermoresponsive,” meaning they respond to heat. At temperatures above 32°C, they release water, shrinking in size. Conversely, when the temperature drops, the hydrogel absorbs water, returning to its original volume. This process mimics muscle movement, making these hydrogels promising as soft actuators for next-gen soft robots.

Accelerated Volume Change
Previously, the slow pace of volume change in thermoresponsive hydrogels limited their practicality. However, Kiel’s materials researchers have taken a cue from nature and integrated a network of microscale tubes into their hydrogel. This approach allows for rapid size changes without sacrificing stability, resulting in the material exerting up to 4,000% more force. This biomimetic design draws inspiration from natural systems like capillaries in humans, optimizing mass and fluid transport in soft materials.
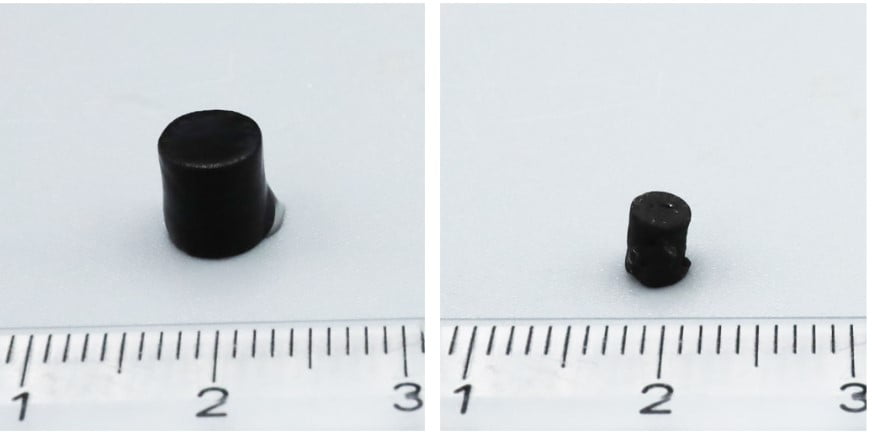
Graphene Coating for Control
To further enhance the material’s usability, an extremely thin graphene coating renders the microscale tubes electrically conductive. This enables control of water transport through the hydrogel using an electric current. The entire volume change process, which previously took weeks, now occurs in just a few hours. Additionally, the material can be controlled wirelessly using directed light, enhancing flexibility and adaptability.
Tailored for Diverse Applications
The researchers have demonstrated the adaptability of the hydrogel by varying the structure of the inner tubes and adjusting the graphene concentration. These modifications alter reaction times and exerted forces, making the material suitable for a range of applications. Professor Nicola Pugno from the University of Trento, an expert in Solid State and Structural Mechanics, contributed to understanding how structural changes impact hydrogel properties. Collaborations with experts from the Helmholtz-Zentrum Hereon and the Technical University of Dresden enriched the research.
Medical Possibilities
The tissue-like properties of this hydrogel open up possibilities in the medical field. Applications could include robot-assisted surgery, artificial tissue construction, or controlled drug-release implants within the human body.
The continued development of thermoresponsive hydrogels with rapid volume change capabilities may bring soft robotics closer to achieving intelligent, adaptable materials inspired by nature. This approach may not only promise advancements in various industries but also may hold the potential for revolutionizing medical applications.